Eurotray® Angle Seam
For Designer, Metallic and Gloss colours, download the ColorCote® special colours brochure.
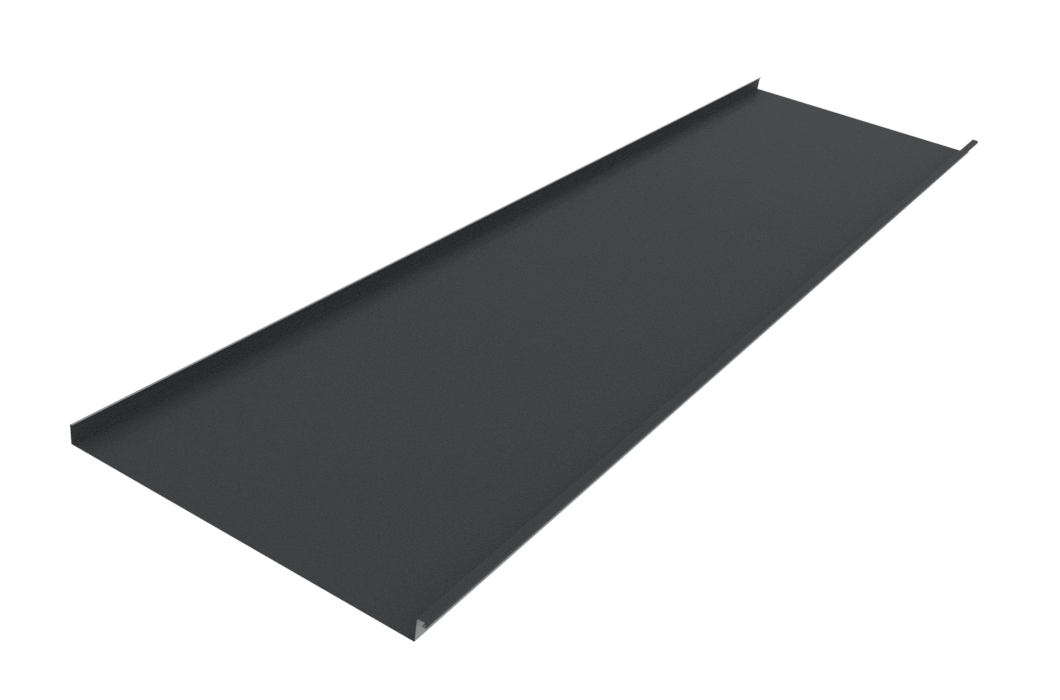
Light Commercial
Commercial
Christchurch
Invercargill
Eurotray® Angle Seam Performance
Looking to add interest to your design or project? Consider the bolder look that Eurotray® Angle Seam offers. This member of the Eurotray® family lends itself well not only as a striking roofing profile - but as an exceptional wall cladding solution as well. In cladding situations, Angle Seam can be run both vertically or horizontally. Angle Seam can also be concave curved.
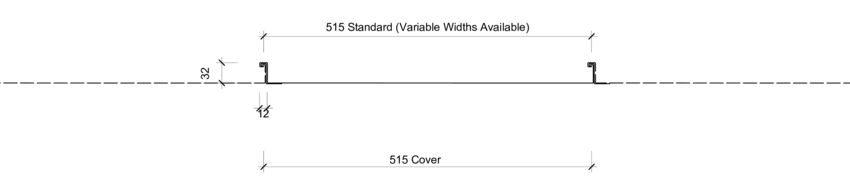
Cover width may vary based on manufacture location. Please consult you local Dimond branch for local cover dimensions
Note:
1. Cover width may vary based on manufacture location. Please consult you local Dimond branch for local cover dimensions
2. Minimum
pitch 3° - In snow loading zones N1-N5 (as
per Section 15 of NZS 3604), please contact the Dimond technical team at rooftech@dimond.co.nz for the minimum
pitch requirements.
Short sheet and flashing considerations
Unless specified otherwise short sheets and flashings will usually be made on an automatic bending Raz machine.
Ensure to state on the order "manual folding required to 10mm minimum bend" when ordering short sheets or flashings because some manufacturing locations have Raz machines with 11-12mm minimum bends.
Sheet Tolerances
Sheet width: ±5mm
Sheet width for aluminium +0, -15mm. If sheet cover widths are critical, advise Dimond Roofing at time of order.
Sheet length: +10, - 0mm. For horizontal wall cladding where notified at time of order of intended use, tighter tolerances can be achieved +3, -0.
(1) Product only available in ColorCote® MagnaFlow™ or Colorsteel® MAXX coated product range
(2) Please contact your Dimond Roofing 0800 Dimond (0800 346 663) for availability.
Roll-forming facilities at: Auckland, Christchurch and Invercargill
Curving facilities: Machine is transportable. For curving restraints check with the local RoofingSmiths.
Sheet lengths: Eurotray® is custom run to order.
Where long sheets are used, consideration must be given to:
- Special transportation licences
- Should be run on-site
- Site access for special lifting equipment
- Fixing techniques to accommodate thermal expansion
Oil Canning
Oil Canning is the visible waviness in the flat areas of metal roofing and walling. Oil canning produces an aesthetic effect inherent in standing seam tray profiles and profiles/flashings with wide flat elements. It does not cause detriment to product performance.
Oil canning can occur during the forming and installation processes and during thermal expansion of the roof sheeting during its life cycle. The effect can be more or less pronounced depending on differing light and sun angle conditions and the coating gloss levels.
For fully supported standing seam tray profiles, oil canning can be reduced by the vented roof underlay (e.g. Tyvek Metal), in addition, backer rods under the tray can also be used.
There are several options to reduce the oil canning effect in tray-type profiles and flashings, for example,
a) increasing the thickness of the material,
b) using stiffening swages in wide flat elements and
c) limiting flat elements to less than 150mm width.
For further information, please refer to the New Zealand Metal Roof and Wall Cladding Code of Practice, Section 12.3.
Relevant Product CAD Details
Below you will find all of the relevant product CAD technical details in .dwg, .pdf & .rvt format.
If you have any questions regarding the details below please contact one of our technical team on 0800 ROOFSPEC.
Eurotray Angle Seam - Horizontal Cladding With Cavity Flush Mounted Window Detai...
Last updated May 2021
Eurotray Angle Seam - Horizontal Cladding With Cavity Window Detail - Sill Flush...
Last updated May 2021
Product Technical Statement
To help you get through the building consent process as quickly as possible, we have developed the Product Technical Statement (PTS) downloads to make it quick and easy for both Architects and Home Owners to access the documentation required.
The PTS downloads hold all of the information that the council requires for a building consent where Dimond product is specified.
Product Brochure
Need a brochure for one of our rainwater profiles? Here you can download our brochure with the basic information and details you need during the decision process.
Below you can download our homeowner’s brochure which includes some of our profiles and basic product information for homeowners when re-roofing or building new.