Advanced Non-Vented
Customizable Thermal Solution
Dimond Advanced Non-Vented - engineered to redefine thermal efficiency with customizable R-values, effectively mitigating condensation challenges in diverse climates.
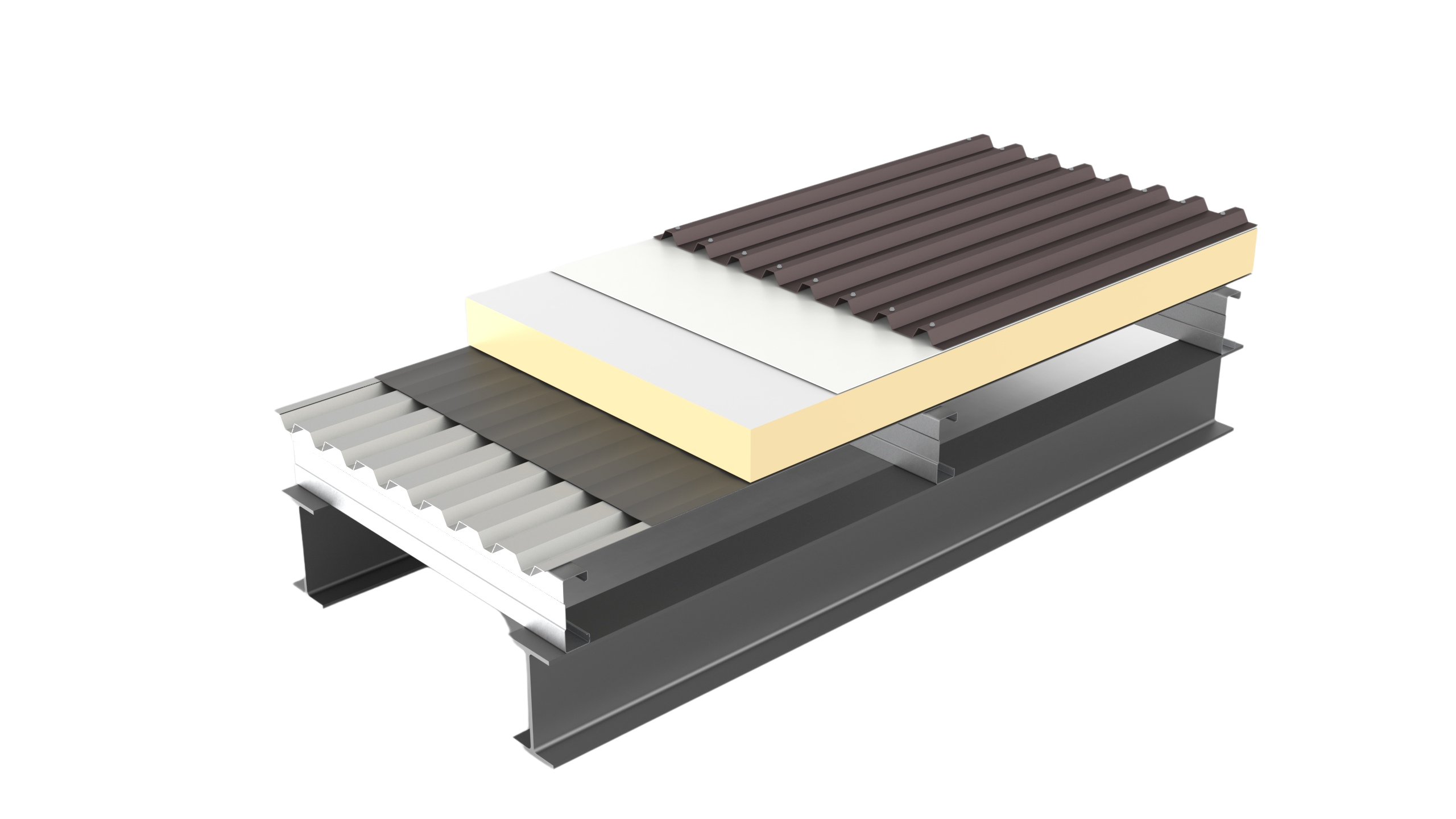
Dimond Advanced Non-Vented, utilizes a two-part water vapour and condensation control system, designed to perform effectively in all environments.
Thermal Performance:
- Utilizes PIR board core with customizable R-values (R2.0 to R7.0), ensuring tailored efficiency.
Condensation Management:
- Features a complete vapour barrier layer, separating internal and external environments to eliminate condensation concerns.
- Includes a two-part water vapour and condensation control system with vapour barrier and underlay.
Construction Timelines:
- Streamlines construction timelines with early close-in capability using Liner Deck and a self-adhesive vapour control layer.
Flexibility:
- Offers design flexibility with various options from the Dimond Range, allowing customization based on base metal, coating, and exposure zone.
Other Features:
- Suitable for all environments and cost-effective compared to the vented system.
- Has limitations on sheet length (up to 25m) due to thermal movement.
- Overcomes composite insulated roof panel limitations.
Limitations:
- Not intended for installation over a plywood liner.
- Roof pitch meets the minimum required pitch for the selected top sheet product.
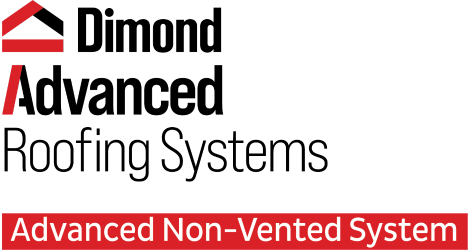
All components in Dimond Advanced Roofing Systems are warranted by their individual manufacturer for use in Dimond Advanced Roofing Systems. Component warranties are subject to the terms and conditions set out by the individual manufacturer. Dimond Advanced Roofing Components must be installed, used, and maintained in accordance with the individual manufacturer’s guidelines.
The Non-Vented Difference
Identifying the difference between Non-Vented and Vented.
We recommend the vented roof rail on roof sheets over 25m and in freezing climates as the vented rail allows the top sheet to expand and retract separately from the components below. Additionally, in freezing conditions, it serves as a cold deck, minimizing the chances of ice damming.
Environmental Challenges
New Zealand's inherently variable climate challenges occupant comfort in buildings, requiring effective insulation and moisture management to maintain year-round comfort and reduce energy consumption. Without the correct systems in place, the fluctuating weather conditions, ranging from hot summers to cold winters, can lead to thermal discomfort and moisture-related issues such as condensation and mould growth. Existing methods often fail to provide custom solutions for effective insulation and vapour barrier needs, resulting in inefficient thermal regulation and increased energy usage.
Addressing the Challenge with the Advanced Non-Vented Solution
Dimond Advanced Non-Vented effectively tackles the challenge of New Zealand's variable climate by providing a ground-breaking solution for thermal performance. Its customizable R-values (R2.0 to R7.0) offer tailored efficiency, ensuring optimal insulation for different climatic conditions. The product eliminates condensation concerns with a complete vapour barrier layer, effectively separating internal and external environments to prevent moisture-related issues such as condensation and mould growth.
Additionally, Dimond Non-Vented streamlines construction timelines with early close-in capability using NPM Liner Deck and a self-adhesive vapour control layer, ensuring efficient installation and minimizing construction-related disruptions. Compliant with Building Code and NZ Metal Roofing Code standards, Dimond Non-Vented assures weather-tightness, while its separable top skin allows precise customization, overcoming the limitations of composite insulated roof panels.
Furthermore, the integration of the Acoustic Board, Audioperf, effortlessly enhances acoustic performance, providing a comprehensive solution for occupant comfort in buildings across New Zealand's variable climate.
Interact with each component in the 3D render below:
A closer look at Advanced Non-Vented
Dimond Base Sheet
Dimond Base Sheet comes in two styles tailored to specific regions: Dimond BB900 for the North Island and Dimond LT7 for the South Island. Crafted from G550 steel, it is available in thicknesses of 0.40mm or 0.55mm BMT, providing sturdy support for roofing projects.'
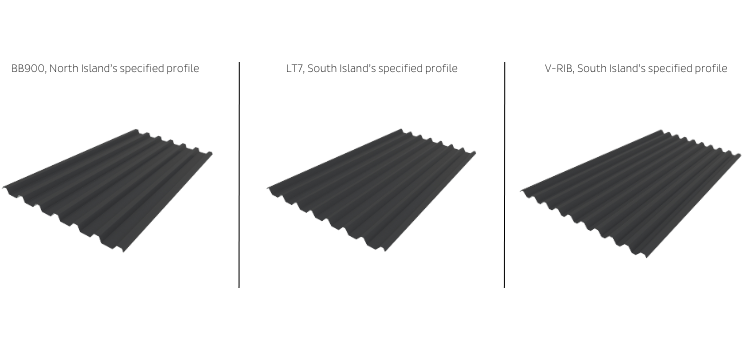
Spans for walls are limited by Serviceability Limit State wind uplift – Refer to Dimond BPIS
*For more information, please refer to Dimond’s website
- Minimum 3° Roof pitch. Max purlin spacing as per the BB900 and LT7 load span charts. Specify coating on steel to match the environment.
- Fix Dimond Base Sheets every 2nd crest into the internal purlin spacings and every crest on sheet ends, using a 12g x 20mm tek (for steel purlins) or a T17x 35mm (for timber purlins).
Refer to Dimond's manufacturer's BPIS and installation data.
Dimond Vapour Barrier
CaVap Alu 1500 UV-AC is an air and vapour barrier consisting of a multilayer aluminium composite, with a tear-resistant fabric reinforcement. The membrane is equipped on its underside with an all-over acrylate adhesive which is covered by a siliconized polyethylene liner.
PIR Insulation Board
Advanced Non-Vented's insulated roof system is available in two brands of high-quality PIR insulation board options, Thermakraft T28 and IKO Enertherm and in multiple thicknesses to suit your required R Value.
Refer to manufacturers' BPIS and installation data in the downloads section.
*Based on PIR only without the additional R value from surface effects and additional Dimond Vented System™ components.
*Based on PIR only without the additional R value from surface effects and additional Advanced Vented System™ components.
Dimond Underlay
Dimond underlay is a choice of Thermakraft Covertek 403 or Pro Clima Solitex Mento 1000 connect.
Refer to manufacturers' technical and installation data to ensure most up-to-date information.
Refer to manufacturers' technical and installation data to ensure most up-to-date information.
Dimond Top Sheet
All Dimond roof profiles can be used as a Dimond Top Sheet and are manufactured out of Pacific Coil Coaters ColorCote or New Zealand Steel COLORSTEEL product.
Product Variations (Thickness, Shape, and General Product Variables)
Refer to Table 2.1A, of the Dimond BPIS, which summarises the general base and top Sheet material options available.
Manufactured using different coatings available from Pacific Coilcoaters or New Zealand Steel depending on the durability required for the environment the roof or wall will be installed in, in accordance with AS/NZS 2728. For more information refer to Table 2.1C of the Dimond BPIS downloaded online at www.dimond.co.nz
Refer to environmental literature available from Pacific Coilcoaters or New Zealand Steel or contact Dimond®
Roofing on 0800 766 377. Duraclad® is recommended for use in special areas such as fertiliser works or very severe marine.
Fixings
Fix Dimond Base Sheets every 2nd crest into the internal purlin spacings and every crest on sheet ends, using a 12g x 20mm tek (for steel purlins) or a T17x 35mm (for timber purlins).
Fix the Dimond Top Sheet using the appropriate length and fixing patten of 12g or 14g screw through the roof system and into the roof or wall structure as per the Dimond BPIS.
Fixings must match or surpass the durability of the material they secure. Additionally, their metal or coating should be compatible with the cladding material if they come into contact. For pre-painted steel products, fasteners must be factory colour-matched before installation.
Screw fasteners need to have adequate length to ensure they penetrate the supporting structure properly. Generally, for screws into timber, a minimum embedment of 30mm is recommended, while screws into steel should engage at least three threads. In severe environments, a minimum Class 4 rating is necessary, whereas very severe environments call for a Class 5 rating.
For further information, refer to the manufacturer's BPIS and installation data.